MASA achieves liftoff with record-setting rocket
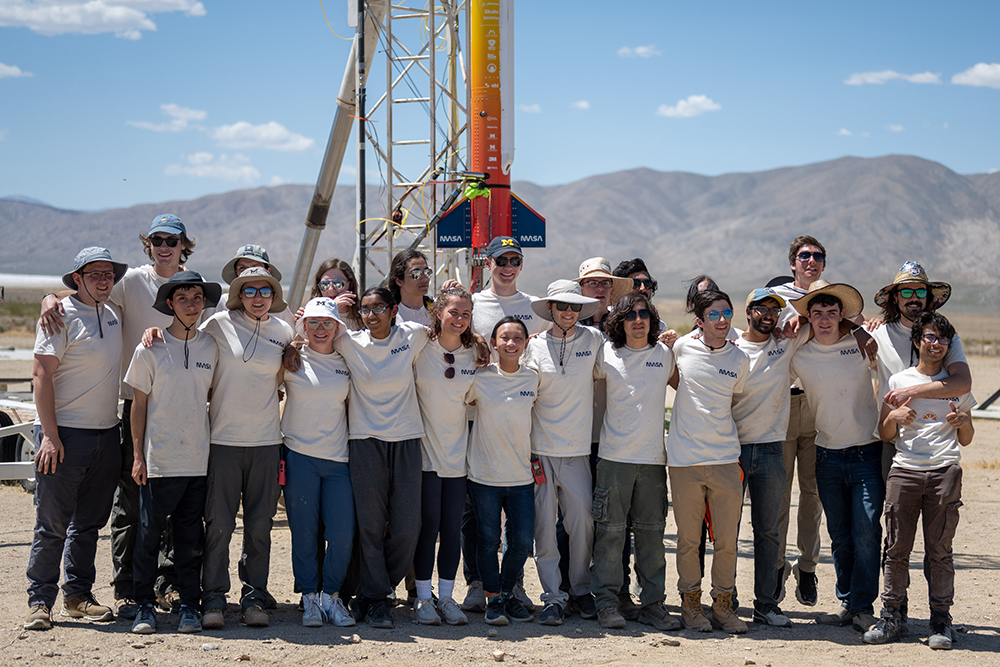
On May 14th, the Michigan Aeronautical Science Association (MASA) successfully launched Clementine, a 20-foot tall liquid bipropellant rocket – the largest to ever be built by college students.
“We wanted to push the limits of what’s possible for a college team to accomplish,” said Evan Eidt, a Computer Engineering undergrad who is MASA’s Avionics Subteam lead.
MASA’s goal is to design, build, and launch liquid-fueled rockets. Through this experience, they focus on providing high quality practical training, which is especially useful for students planning to pursue careers in industry.
“I think we have some of the best collegiate rocket engineers in the world on this team,” Eidt said. “I’m so grateful that we can learn about these technologies, because it’s going to help us to do great things in the future.”
I’m so grateful that we can learn about these technologies, because it’s going to help us to do great things in the future.
Evan Eidt, MASA Avionics Subteam Lead
MASA currently operates on a two-year cycle. The first year is focused on designing and testing various technologies and components, and the second year is construction and launch. While their rockets are not the type that would send supplies or astronauts to space, they would be suitable for Earth-bound missions, such as depositing an atmospheric sensing device at high altitudes.
Since their rocket is so large, MASA has a separate space in the GFL building for construction, in addition to an assembly area for larger systems in the Wilson Student Team Project Center. This year, they completed their rocket integration and vertical testing out at MCity. They used liquid nitrogen and water instead of live propellants, which allowed them to test the fluid system and identify bugs in the electrical and software systems.
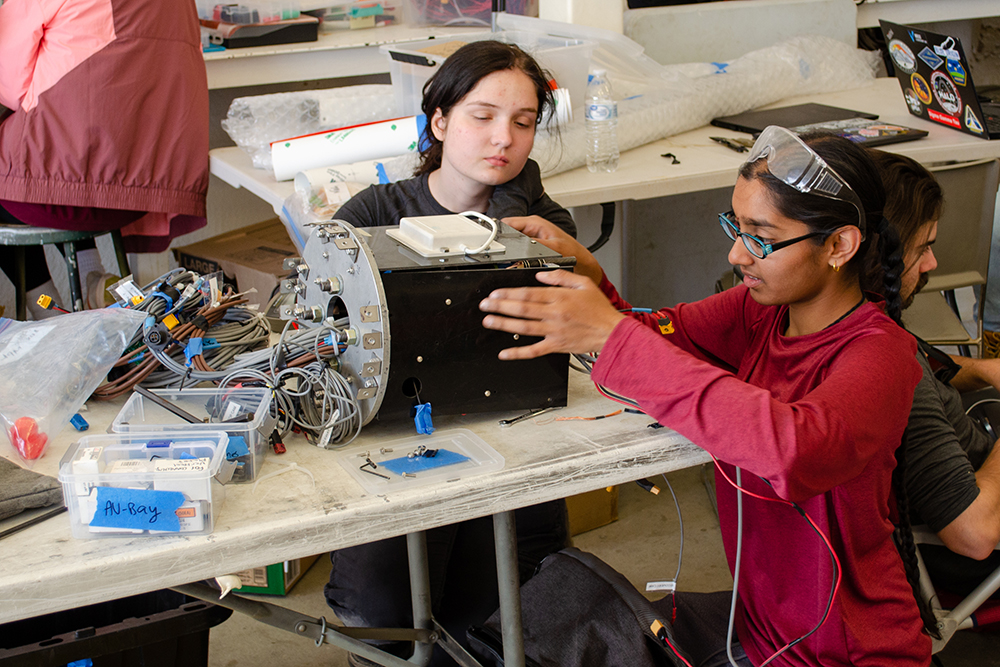
“People know about the aerodynamics or the propulsion side of rockets, but they don’t often think about all the electronics that drive the system,” Eidt said. “For us, there are two major electronic elements: the ground support side and the rocket avionics side.”
The ground support team conducts coldflow and hotfire tests and manages the fluid systems, which requires high fidelity data acquisition systems. It also supports the propellant filling and pressurization steps of launch.
“Those systems have to be able to collect data very fast and have good control systems,” Eidt said. “For example, we might have to actuate some valve and record pressures at a high rate to accurately control tank pressures.”
The rocket avionics group focuses on regulating various functions, such as keeping the fuel tanks at a constant pressure by designing control algorithms. They’re also responsible for managing the radio communication and the camera systems. They design their own custom boards for a variety of applications, such as battery management, and they provide their own firmware as well.
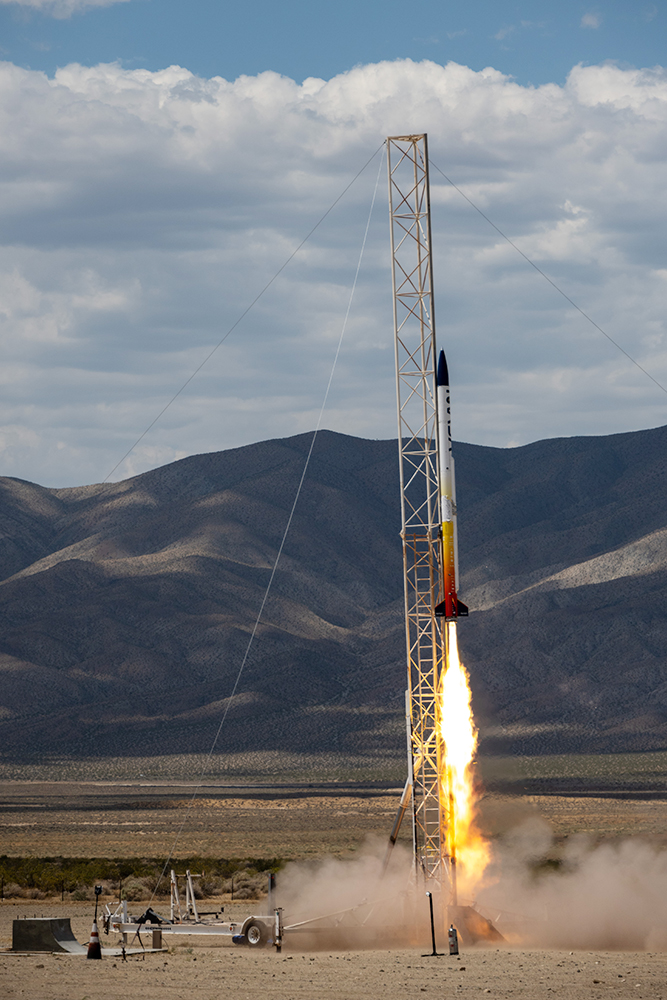
“As a freshman, I was shocked that I was allowed and able to make a board myself,” Eidt said. “So I really loved getting the hands-on electrical and software experience.”
In addition to their work on campus, MASA conducted their hotfire test– a one-second engine burn with live propellants – at the Reaction Research Society site out in the Mojave Desert, which is near the Friends of Amateur Rocketry site where they later conducted the official launch.
Around 100 team members contributed to the project over the past two years, and of those, a little more than 20 (including Eidt) were selected to serve as the launch crew. The launch crew had nearly a week at the site to prepare for launch. They set up stations to assemble the rocket, which had to be shipped in parts, and made use of a semi-clean room, where they could protect more delicate components from the dust. They also set up their mission control section, which included their computers and camera monitors.
“We’d drive out to the site early in the morning,” Eidt said. “It was hot, and there was a lot of dust and a lot of bugs.”
Like with NASA, the weather conditions have to be right for MASA to launch.
“The biggest issue for us in the desert is wind,” Eidt said. “If we launch in winds that are too strong, the rocket won’t be stable. The direction of the wind also matters – we don’t want the rocket to get blown into some nearby town or back toward us.”
But the wind patterns in that area of the desert were reliably predictable, so the team was able to plan for their best launch window. In addition to the launch team, dozens of other team members, family, and friends, as well as MASA alumni in the area, came out to witness the event.
“Seeing something that I’ve spent the last two years on go up in the air was absolutely awesome,” Eidt said.
The successful launch came after years of hard work and recovery following a MASA incident a few years ago that, during a hotfire test in Ann Arbor, experienced a failed ignition that produced a very loud bang. While no personnel were harmed, the team temporarily suspended operations out of an abundance of caution.
“That was one of the biggest, most important lessons that we ever had,” Eidt said. “We knew that could never happen again, because we weren’t happy, and the residents of Ann Arbor definitely weren’t happy. We value our relationship with our community and local partners and wanted to prevent future incidents.”
The team completely changed their leadership structure, their operating procedures, and their design methodologies. Today, they focus on transparency and rigorous safety reviews and checks for every step of the process. They no longer hotfire test in Ann Arbor, or any residential area.
“We head out to the middle of nowhere now, which is a lot safer,” Eidt said. “But because it’s so expensive to get out there, we can only hotfire test about once a year. This means we have to prepare really well with coldflow testing and our designs have to be really solid.”
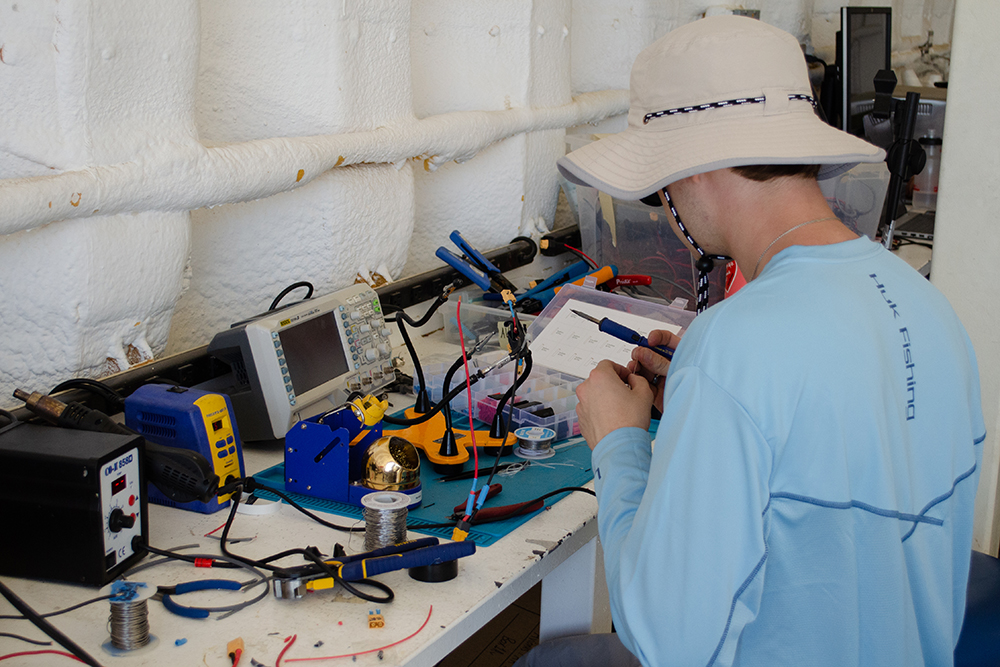
The team is already focusing on their next rocket, Limelight. Their goal is to use new technologies to break the liquid altitude record.
Eidt is also planning the future of electronic teams. The rocket avionics group will switch from operating with one primary engine controller in a flight computer to a network of multiple boards distributed throughout the rocket that are connected via ethernet. The ground control group will also be switching from custom design boards to a modular design for higher resolution data.
“I’m really excited to help design those systems, because they’ll have higher data capabilities and have less failure risk,” Eidt said. “And I want to make sure our methods are really well thought-out and well documented, so it will be useful for the team for years to come.”